تفاوت گالوانیزه گرم و سرد چیست؟ کدامیک مناسبتر است؟
گالوانیزه، آهنی است که با روی پوشیده شده و به مقاومت بالا معروف است. روی باعث میشود آهن از هرگونه زنگزدگی در امان بماند و به عمر آن اضافه شود. گالوانیزه به دلیل مقاومتی که دارد در جوامع مختلف دارای محبوبیت است و قدمت آن را میتوان به حدود 150 سال پیش نسبت داد. امروزه مقدار زیادی از فلز روی تولیدی در جهان برای پوشش گالوانیزه مصرف میشود. به فرآیند گالوانیزه شدن، گالوانیزاسیون میگویند.
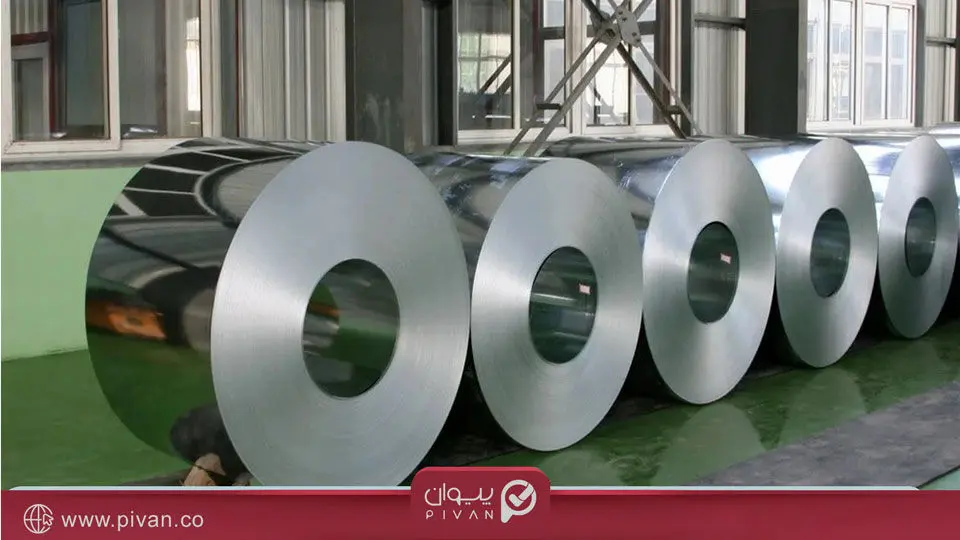

فرو رفتن آهن در مخزنی از روی مذاب شده جهت پوششدهی سطح آهن توسط روی را گالوانیزاسیون با روش غوطهوری گرم میگویند. در این روش از آهن در برابر زنگزدگی و خوردگی محافظت میشود. این روش یکی از روشهای پرکاربرد در برابر زنگزدگی میباشد که در گذشتهها نیز از این روش برای گالوانیزه کردن استفاده میشد. روش گالوانیزاسیون نسبت به روشهای دیگری که برای جلوگیری از زنگزدگی استفاده میشود هزینه کمتری دارد. لایه محافظ شکل گرفته دو ویژگی مهم را دارد. ۱- چسبندگی به فلز اولیه ۲- مقاوم بودن در برابر اصطحکاک.
Hot galvanizing
گالوانیزه گرم یکی از روشهای گالوانیزاسیون است که به منظور جلوگیری از خوردگی و آسیب قطعات فلزی انجام میشود. گالوانیزه گرم با فرو بردن قطعات آهنی یا فولادی در یک وان مذاب روی با دمایی حدود ۴۶۰ درجه سانتیگراد جهت پوشش دهی قطعات صورت میگیرد.
سه مرحله اساسی در فرآیند گالوانیزه گرم شامل آمادهسازی سطح، گالوانیزه و بازرسی است. این روند ذاتاً ساده است و مزایای ویژهای نسبت به سایر روشهای محافظت در برابر خوردگی دارد. در این روش آهن و فولاد به طور متالورژیکی با روی مذاب واکنش نشان میدهند تا یک پوشش آلیاژی محکم با مقاومت بالا در برابر خوردگی ایجاد کنند. گالوانیزه کردن فلز به آن خاصیت ضد خوردگی میبخشد. بدون پوشش رویی محافظ فلز در معرض آب و هوا باقی قرار گرفته و به طور بالقوه اکسید میشود و خیلی سریعتر از بین میرود. فولاد گالوانیزه گزینهای مقرون به صرفه برای استفاده به جای موادی مانند فولاد ضد زنگ یا آلومینیوم به منظور جلوگیری از خوردگی است.
فرآیند گالوانیزهسازی گرم
فرآیند گالوانیزه غوطه وری گرم نسبتاً ساده است. این فرآیند شامل تمیز کردن فولاد و غوطهور کردن آن در روی مذاب برای به دست آوردن یک پوشش است. در طی فرآیند، یک پوشش پیوند متالورژی تشکیل میشود که از فولاد در برابر محیطهای سخت، چه خارجی و چه داخلی محافظت میکند. فولاد گالوانیزه به طور گستردهای در کاربردهایی مورد استفاده قرار میگیرد که مقاومت در برابر خوردگی بدون هزینه فولاد ضد زنگ مورد نیاز است و میتوان آن را با الگوی متبلور روی سطح شناسایی کرد. گالوانیزه سازی احتمالاً دوستانهترین فرآیند موجود در محیطزیست برای جلوگیری از خوردگی است. گالوانیزه غوطهوری گرم یک فرآیند بسیار ساده است که محافظت طولانی مدت در برابر خوردگی را برای فولاد فراهم میکند.
تاریخچه
در سال ۱۷۴۲، شیمیدان فرانسوی، پائول ژاک مالوئین، طی سخنرانی در آکادمی رویال فرانسه، روشی برای پوشش آهن با فرو بردن آن در روی مذاب توصیف کرد. در سال ۱۷۷۲، لوئیجیگالوانی (ایتالیا)، فرآیند الکتروشیمیایی بین فلزات را کشف کرد. در سال ۱۸۰۱، آلساندرو ولتا با کشف الکترو پتانسیل بین دو فلز و ایجاد یک سلول خورنده تحقیقات مربوط به گالوانیزه را ادامه داد. در سال ۱۸۳۶ شیمیدان فرانسوی استانیسلاساس سورل برای کشف روش پوشش آهن با روی حق ثبت اختراع را بدست آورد. در این روش پس از پاک کردن فلز با اسید سولفوریک ۹٪ (H2SO4) قطعات با کلرید آمونیوم (NH4Cl) فلاکس زنی میشوند. فرآیندهای شیمیایی، خمیر و کاغذ، اتومبیل و صنایع حمل و نقل تنها معدودی از برنامههایی هستند که در طول تاریخ برای کنترل خوردگی از گالوانیزه استفاده میکنند. گالوانیزه گرم نیز دارای سابقه طولانی و اثبات شده رو به رشد و موفق در برنامههای مختلف در سراسر جهان است.
مراحل آماده سازی سطح
هنگامی که قطعات فولادی یا آهنی به تأسیسات گالوانیزه میرسد، آنها را به سیم آویزان کرده یا در سیستم رکاب قرار میدهند که با استفاده از جرثقیل بتوان آنها را جابجا کرد. سپس قطعات فلزی از یک سری مراحل تمیزکاری عبور میکنند مثلا چربیزدایی باعث حذف خاک، روغن و باقیماندههای آلی میشود، در حالی که حمام اسیدی اکسید آهن و پوستهها را از بین میبرد. مرحله آماده سازی نهایی شامل فلاکس زنی است که باعث میشود اکسیدهای باقیمانده برداشته شود و فولاد و آهن را با یک لایه محافظ بپوشاند تا از تشکیل اکسید بیشتر قبل از گالوانیزه جلوگیری کند. آماده سازی مناسب سطح قطعات بسیار مهم است، زیرا روی با قطعات کثیف واکنش نشان نمیدهد.
مطالب مرتبط: استعلام قیمت ورق روغنی امروز در بازار
گالوانیزه کردن
پس از آمادهسازی سطح، فولاد و آهن در حمام مذاب روی فرو میروند. این قطعات با زاویهای درون حمام فرو میروند که باعث میشود روی در کل قطعه جریان یابد. در حالی که قطعات در روی غوطهور هستند، آهن و فولاد به طور متالورژیکی با روی واکنش نشان میدهد تا یک سری لایههای میان فلزی روی در سطح آنها تشکیل شود.
بازرسی
مرحله آخر بازرسی پوشش است. با استفاده از یک بازرسی بصری میتوان به صورت دقیق کیفیت پوشش را مشخص کرد. علاوه بر این، میتوان از یک ضخامت سنج مغناطیسی برای تأیید ضخامت پوشش مطابق با الزامات استاندارد استفاده کرد.
مراحل فرآیند گالوانیزه گرم
چرخه تمیز کردن: واکنش گالوانیزه شدن فقط در یک سطح تمیز شیمیایی رخ خواهد داد. به طور مشترک در اکثر فرآیندهای پوشش روی، راز دستیابی به یک پوشش با کیفیت خوب سطح تمیز است. ضروری است که ماده مورد استفاده قبل از گالوانیزهسازی عاری از چربی، کثیفی و یا هرچیز دیگری باشد. این نوع آلودگیها با فرآیندهای مختلف برطرف میشود و روش معمول برای چربیزدایی این است که ابتدا با استفاده از محلول قلیایی یا اسیدی که ماده در آن غوطهور میشود، چربیزدایی انجام میگیرد. سپس ماده گالوانیزه شده را در آب سرد شستشو میدهند تا از بقیه آلودگیهای پاک شود. سپس آن را در اسید کلریدریک در دمای محیط غوطهور میکنند تا زنگزدگیها از بین برود. سربارههای جوشکاری، رنگ و چربیهای سنگین با این مراحل تمیز کردن برطرف نمیشوند و باید قبل از ارسال کار به محیط گالوانیزه توسط سازنده برداشته شوند.
روش شار: این روش معمولاً با غوطهور کردن فلز در محلول شار (معمولاً حدود ۳۰٪ کلرید آمونیوم روی در حدود ۶۵-۸۰ درجه سانتی گراد) اعمال میشود. عملیات شار آخرین آثار اکسید از سطح را از بین میبرد و به روی مذاب اجازه میدهد تا فولاد را کاملا خیس کند.
فرآیند گالوانیزه سازی: هنگامی که اجزای آهن یا فولاد کاملا تمیز شده در فلز روی ذوب شده (که معمولاً در حدود ۴۵۰ درجه سانتیگراد است) فرو میروند، یک سری از لایههای آلیاژ روی و آهن با واکنش متالورژی بین آهن و روی تشکیل میشوند. سرعت واکنش بین فولاد و روی به طور معمول نسبت به زمان پارابولیک (Parabolic) است و بنابراین سرعت واکنش اولیه بسیار سریع است و تحرک قابل توجهی در حمام روی مشاهده میشود. ضخامت اصلی پوشش در این دوره تشکیل میشود. پس از آن، سرعت واکنش کاهش مییابد و ضخامت پوشش حتی اگر ماده برای مدت زمان طولانی در حمام باشد، به طور قابل توجهی افزایش نمییابد.
تیمار: فرآیند پس از گالوانیزه میتواند شامل خنکسازی در آب یا خنک کننده هوا باشد. شرایط موجود در کارخانه گالوانیزه مانند دما، رطوبت و کیفیت هوا بر کیفیت پوشش گالوانیزه تأثیر نمیگذارد. در مقابل، این روشها برای نقاشی با کیفیت خوب بسیار مهم هستند. برای تیمار محصولات گالوانیزه میتوان از رنگ یا پوششهای پودر برای زیبایی یا محافظت بیشتر در مواردی که محیط بسیار تهاجمی است استفاده کرد. برای به حداقل رساندن وقوع لکه ذخیرهسازی مرطوب، ممکن است از پوششهای شیمیایی و سیستمهای سد کننده دیگر نیز استفاده شود.
مزایای گالوانیزه گرم
گالوانیزه گرم مزایای بسیاری برای قطعات فولادی فراهم میکند. لایههای آلیاژ روی (آهن متالورژی) نه تنها مانعی بین فولاد و محیط ایجاد میکنند، بلکه از نظر کاتدی نیز از فولاد محافظت میکند. حافظت کاتدی ارائه شده توسط روی به معنای پوشش گالوانیزه است که خود را برای محافظت از فولاد زیرین در برابر خوردگی قربانی میکند. روکش محکم چسبنده ایجاد شده استحکامی حدود 600 / 3psi دارد و در برابر سایش بسیار مقاوم است، زیرا لایههای بین فلزی سختتر از فولاد پایه هستند. بنابراین حتی اگر این پوشش آسیب دیده باشد، پوشش روی قربانی باعث میشود تا فولاد در معرض تا ۴/۱ اینچ محافظت نشود. علاوه بر محافظت کاتدی که توسط گالوانیزه گرم ارائه میشود، چند ویژگی دیگر این پوشش باعث افزایش ماندگاری قطعات فلزی میشود. واکنش آبکاری گالوانیزه یک فرایند انتشاری است، به این معنی که پوشش به صورت عمودی بر روی سطح ایجاد میشود و اطمینان حاصل میکند که همه گوشهها و لبهها دارای حداقل ضخامتی برابر با سطوح مسطح هستند. علاوه بر این، غوطهوری کامل در حمام روی، پوشش کامل فولاد و آهن از جمله فضای داخلی سازههای توخالی را نیز فراهم میکند.
بیشتر بدانید: لوله درزدار چیست؟
Cold Galvanizing
گالوانیزه سرد یکی از راههای محفاظت از فلزات است که بر قیمت آهنآلات موثر بوده و کاربردهای بسیار زیادی در صنعت دارد. این فرآیند تفاوت زیادی با دیگر روشهای گالوانیزاسیون دارد و در آن از روی غنی شده با غلظت حداقل 92 درصد استفاده میشود. برای پوششدهی قطعات بهوسیله گالوانیزه سرد ابزارهایی همچون قلممو، اسپری یا پیستوله را به کار میگیرند و سطح فلز را با روی غنی شده پوششدهی میکنند. گالوانیزاسیون سرد در موارد و صنایع بسیاری کاربرد دارد. شماری از این موارد شامل کاربرد در خودروسازی، کارایی در قطعه سازی، کاربرد در تولید ورق رنگی و شیروانی، استفاده در تولید مفتول گالوانیزه سرد برای توری مرغی و در نهایت کاربرد در تولید قطعات رزوهدار همچون پیچ و مهره میشود.
مزایای گالوانیزاسیون به روش سرد
گالوانیزه سرد مزایای بسیاری دارد که منجر به محبوبیت آن میان مصرفکنندگان شده است. زحمت کم انجام فرآیند گالوانیزه سرد یا به عبارت دیگر، پیچیدگی پایین آن و عدم نیاز به تجهیزات ویژه، از مزایای این روش میباشد. از دیگر مزایای گالوانیزه سرد میتوان به سطح براق و درخشان آن اشاره کرد. نظر به این امر، در مواردی که زیبایی ظاهری اهمیت بسیاری دارد، از گالوانیزه سرد استفاده میشود. در گالوانیزه سرد به علت آنکه از تجهیزات مخصوص استفاده نمیشود و حجم مواد مصرفی در آن بالا نیست، هدر رفت مواد اولیه در آن پایین است. گالوانیزاسیون به روش سرد، در زمان صرفهجویی بسیاری میکند. گالوانیزه سرد صرفه اقتصادی بسیار خوبی داشته و مقرون به صرفه است.
معایب گالوانیزاسیون سرد
در کنار تمامی مزایایی که برای گالوانیزاسیون سرد گفته شد، معایبی نیز برای این فرآیند وجود دارد. یکی از بزرگترین معایب این روش، دوام و مقاومت پایین آن در برابر خوردگی، نسبت به دیگر روشهای گالوانیزاسیون است. این امر نیز به علت عدم پیوند خوردن با فلز در سطح شیمیایی میباشد. به علت پایین بودن ضخامت این پوشش، بهراحتی جدا میشود. در نتیجه در محیطهایی که رطوبت بسیاری وجود دارد، این روش کارایی بسیاری ندارد. یکی دیگر از معایب این روش، انتشار در آلودگی است. آلایندههای گالوانیزه سرد شامل بخشهایی از مواد زائد آبکاری، اسیدهای ترش و مواد زائد مایع منفعلسازی خواهند بود که منجر به آسیب به محیطزیست میشود.